These are the 10 main steps process for manufacturing a complete garment. Every step may have more sub-steps. Making a complete garment is not an easy job after all.
GARMENT MANUFACTURING PROCESS
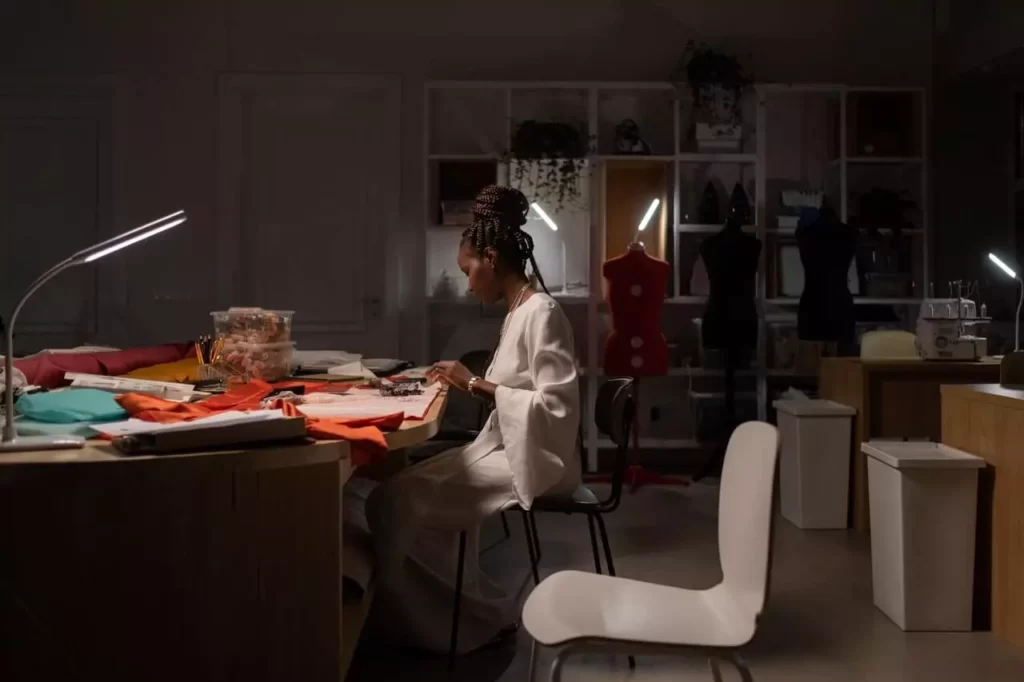
10 Steps to Make a Complete Garment
Time Needed: About 21 Days
- 1. Finalized Design: Getting an idea to make the final design the whole process can be time-consuming. And these are the first step before jumping to make a garment. You can’t make a garment on the craze.
- 2. Selection of Fabric: The exact selection of the right fabric accordingly theme is the starting of an excellent garment. A professional fashion designer can identify the fabric by feeling it.
- 3. Preparation of Fabric: Now that we chose the fabric, it’s time to prepare it. It is important for laying patterns correctly. A raw fabric from the market is not necessarily have undergone a shrinking process during manufacture to prevent further shrinking after washing or cleaning or cut at a straight line.
- 4.Layout: After making the pattern, it needs to place on the fabric in a way so wastage shall be minimum. And that is why the preparation of fabric is important before laying the patterns. There is various layout of laying patterns discussed below.
- 5. Marking: After placing the patterns in chosen layout fix the pattern pieces on the fabric with fine-quality pins. Marking shall be done properly to cut the fabric in nice lines.
- 6. Cutting: For cutting the fabric use good quality scissors. Cut at the exact markings you made. After finishing shift all notch marks from the pattern to the fabric.
- 7. Manufacturing (Embroidery-Sewing): After cutting now it’s time to stitch the fabric pieces according to the size and color for making a full garment. Embroidery is an extra feature that can be added if your client wants it.
- 8. Garment Inspection: After manufacturing the garment you need extra time to inspect the whole garment accurately. This is a very important step because in this stage you need to correct all the mistakes it has.
- 9. Finishing: In this step, you need to do the finishing steps discussed below before packing the garment. This is the final touch.
- 10. Packing and Shipment: Properly fold the garment then pack it for shipping.
1. Finalized Design
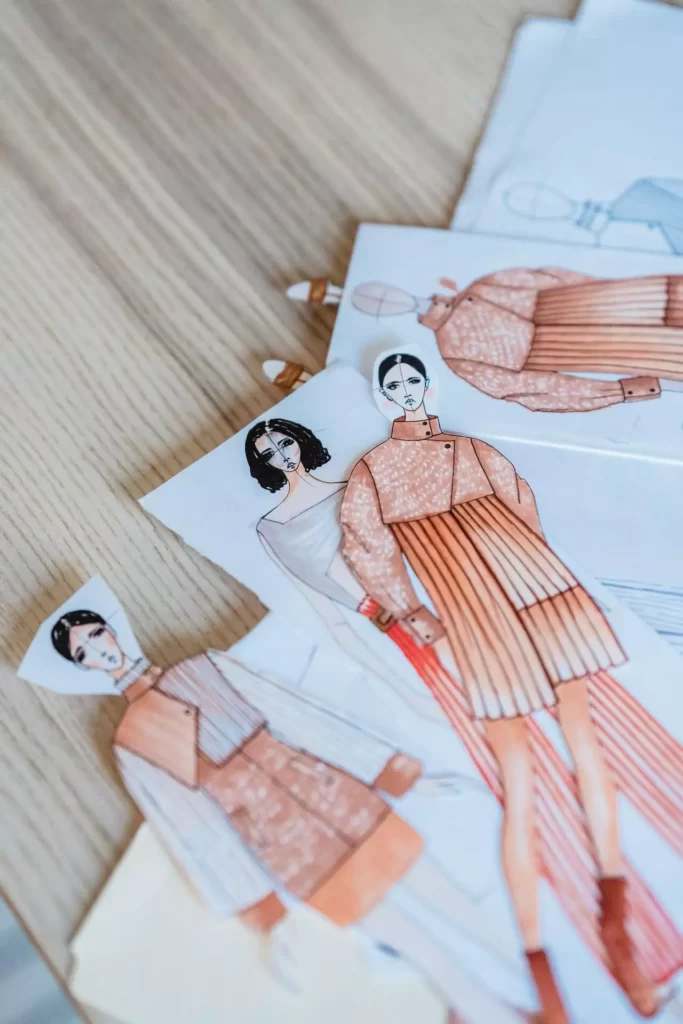
This is the first step of the garment manufacturing process, or rather I’ll say the main step before jumping to manufacturing. Design involves research, getting an idea, idea development, getting a concept of design, final design. Research before creating your project. What kind of design your client wants or is suitable according to the occasion. You can get ideas from nature, from people around us, from various kinds of tribes, cultures. Now that you have gotten an idea, develop your idea. Be creative as much you can or need to. Fashion would not always follow rules but get a lot of inspiration from anywhere you can. You may want to maintain the originality of your design because that always inspires people. Give your ideas multiple sketches. Make your final Design.
2. Selection of Fabric
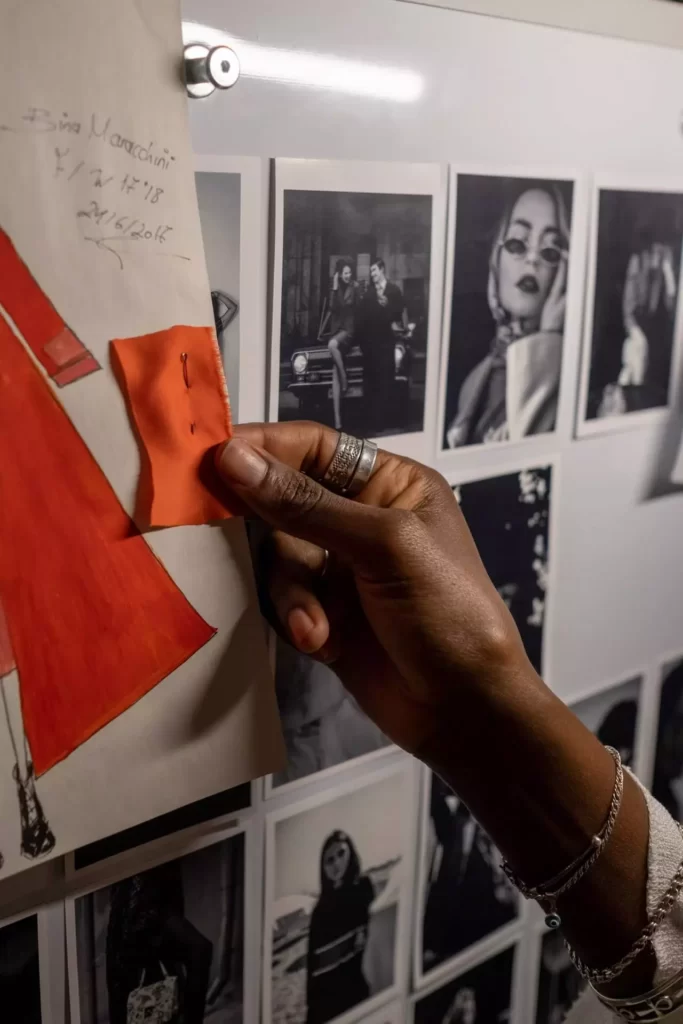
Nobody becomes a professional in one day. You need to develop the right fabric selection skill by understanding and analyzing various fabrics in the market.
Fabrics are three types according to their weights.
Lightweight: Voile, Cheesecloth, Silks, Chiffon, Organza, Crepe, Linen, etc.
Medium Weight: Poplin, Cambric, Satin, Oxford, Calico, Velvet, etc.
Heavyweight: Corduroy, Gabardine, Casement, Canvas, Denim, Suede, Wool Tweed, etc.
If you are a beginner and confused about fabric it’s better to choose a medium-weight fabric. If you choose light or heavyweight fabric they will be harder to control and sew. You may handle lightweight sheer fabrics like Organza, Chiffon by putting paper underneath.
If you’re making the garment for a client, keep the client’s choice in mind. You also need to consider the occasion, season, age, and sometimes the gender for choosing a color (If the client wants). For example, if you’re making a garment for a kid, you shall choose the softer and lighter fabric. For youth and young you can choose denim. It’s not like denim is not for elders but it should be according to the client, occasion, season, even place. For example, in winter it’s better to choose heavy materials even for children.
3. Preparation of Fabric
Strengthen your fabric and prepare so that it will not shrink after washing.
▶ Straightening of Fabric
For straightening a fiber follow the steps below.
a. Tearing
For tightly knitted medium to heavy cotton, you can give a straight cut at one of the selvages to tear the fabric. Don’t use it on embroidered or any kind of jacquard fabrics. Jacquard fabrics can be made from various types of fibers with thicker, heavy, complex knits.
b. Pulling
For loosely knitted soft, light fabric you can pull out a thread through the width. Then cut it. For delicate fabrics follow this method.
▶ Blocking
During the manufacturing of fabric, it goes through various processes which may cause stretching. If so, grain lines will not be at right angles. Through blocking, we need to adjust the shape of the fabric. It is an important step before we jump to placing the patterns. Notice where the fabric is overstretched then you have to stretch it to the opposite direction to get a well-angled grain line. Then press the fabric.
▶ Preshrinking
To prevent shrinking after washing a fabric you must do preshrinking. After manufacturing a fabric it may not go through the shrinking process, so you have to do it. Soak the fabrics in hot water for three-four hours then wash them with detergent in hot water again. It must shrink the fabric. Natural fabrics tend to shrink more than artificial man-made fabrics.
▶ Identifying the right and wrong sides of the fabric
If you’re making a garment, knowing the right and wrong sides of the fabric is very important. You may think it is very easy to identify but some fabrics look the same on both sides. It is easy to say the wrong side of a garment rather than a piece of fabric though.
Follow the steps:
- If both sides look the same feel the texture. The right side should be smoother, polished, and shiny as compared to the wrong side.
- The hem end is smoother on the right side and rough on the wrong side.
- In printed fabrics, the printing mark will be darker and clearer.
- For knitted fabrics, knitting will be prominant, stronger. On the wrong side, you will see uncut threads.
- Still, if both side look and feel the same choose any side then mark it. Place all your patterns on that side later. It means the material does not have different sides.
▶ Directional and Unidirectional Designs
- Notice the design of the fabric. It may have variant designs. Notice the flow of designs. In some fabrics, designs flow in all directions from an emphasis point. Some designs have a specific direction. These are directional fabrics and others are unidirectional designs. Designs like animals, or any recognized things have a direction. Human printing, bird, floral, words printing, etc. For laying patterns keep in mind to keep all the pattern pieces in a specific direction.
- Pile fabrics like velvet, corduroy need special attention. Cut all the patterns in the same direction for these kinds of fabrics. Pile or napped fabrics may have piles running in both directions. Cutting pattern pieces in different directions may result different shades of the same color. This occurs due to the reflection of light.
4. Layout
The layout is the process for placement of pattern pieces for making a garment. Marker plan is another name for layout. Why do we need to make a marker plan? The marker plan helps to calculate the amount of fabric you will need and ensure the supreme usage and minimum wastage of your precious fabric. Look below to know different types of layouts for placing patterns. Choose wisely.
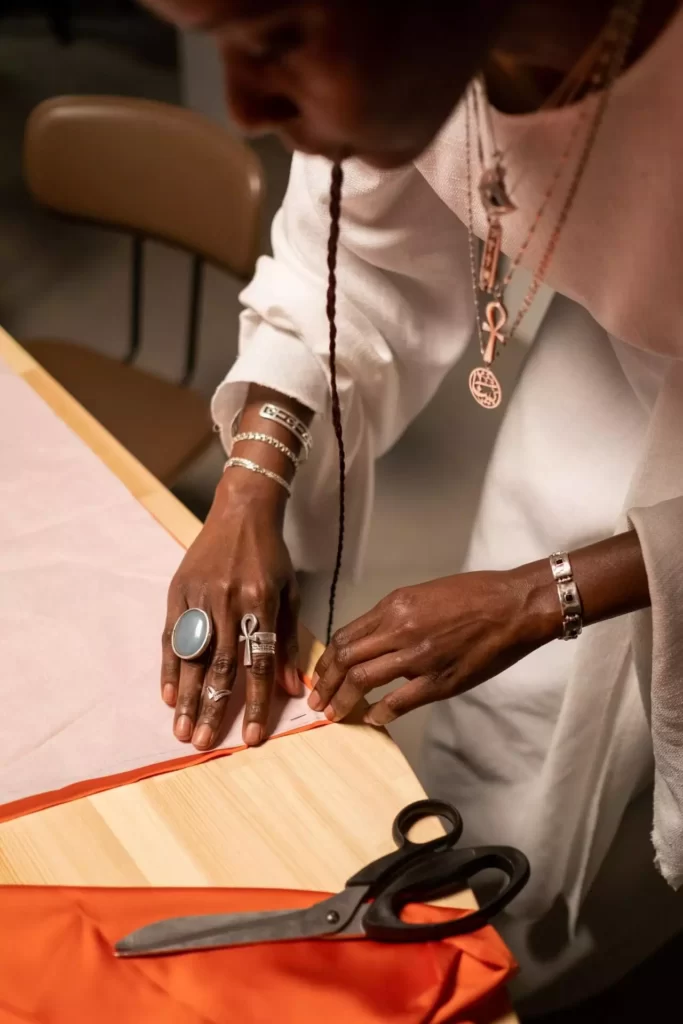
Open Layout
The open layout is the easiest layout for beginners without any fold. Lay the fabric and patterns on the table from left to right one after another. You may use it for all kinds of patterns but especially use it when your fabric is sheer, slippery, or knitted fabrics and for those designs with different left and right patterns. Industries use this method most of the time because at the same time they fashioned multiple layers of fabrics.
Folded Layout
Fold the fabric in half lengthwise or breadthwise. It is necessary to align the selvages so that they exactly meet each other if you fold lengthwise. Fold the fabric facing on the right side and the wrong side is out. Do the markings on the wrong side.
If you cut the fabric in one direction, you may need more fabric, thus it will cost more and will not be very economical. As long as you can lay pattern pieces in both directions that will reduce fabric cost and will be more profitable. Assuming that you use multiple fabrics, then you will require more than one layout. Read below for depth information on various folded layouts.
a. Lengthwise Fold
∎ Lengthwise Center Fold
As the name is suggesting, fold the fabric in the lengthwise direction to bring the selvages together. The selvages of both sides are placed one on top of the other and folded in the middle. It will form a fold at the center. Place all the folded patterns along this fold. For different types of dresses, shirts, blouses you can use this folding method. If you need to cut on the fold of the front and the back of a garment, use this layout.
∎ Off-Centre Lengthwise Fold
Another lengthwise fold is the Off-center lengthwise fold. Here we don’t fold the fabric to bring the selvage together. The essential diameter required for the patterns is us. For small patterns of any garments, you may use this.
b. Crosswise Fold
∎ Crosswise Outer Fold
As you dis lengthwise centerfold, you will do crosswise centerfold but in a crosswise direction not in the lengthwise direction. If the patterns are too narrow to fit lengthwise this folding method is the best. If you need special effects for any garments with different materials where it’s difficult to fit in the lengthwise fold, you can use it.
∎ Off Centre Crosswise Fold
Fold the fabric in the cross-grain for an off-center crosswise folding layout. The fold is straight to the selvage. When a part of the garment needs special effects, or in collars, you may cut in crosswise grain.
c. Double Fold or Combination Fold
As the name is suggesting this is a combination fold. A combination fold is when you fold the fabric both in lengthwise and crosswise grains. For garments that have no openings in the front and back you may use a double fold.
d. Special Layouts
There are some special layouts I’ll not cover in this section. Those are with striped, bold, asymmetric designs.
5. Marking
Markings are only done after placing patterns on the opposite side of the fabric. After folding Pin or staple the folded edges, as shown in the above picture. You may also use adhesive paper. An adhesive paper sticks with the top layer of fabric. Check if the grain lines of all pattern pieces are parallel to the selvage of the fabric. Marking can be done manually by a pencil, pen, or with tailor’s chalk or with a computerized technique. Always mark on the opposite side of the fabric, so no mark will be visible on the right side.
There are special printing symbols on any marker paper, which helps to position components accordingly to grain lines. Markings guide measures, ranges. After complete marking cutting operations are done in the cutting room.
6. Cutting
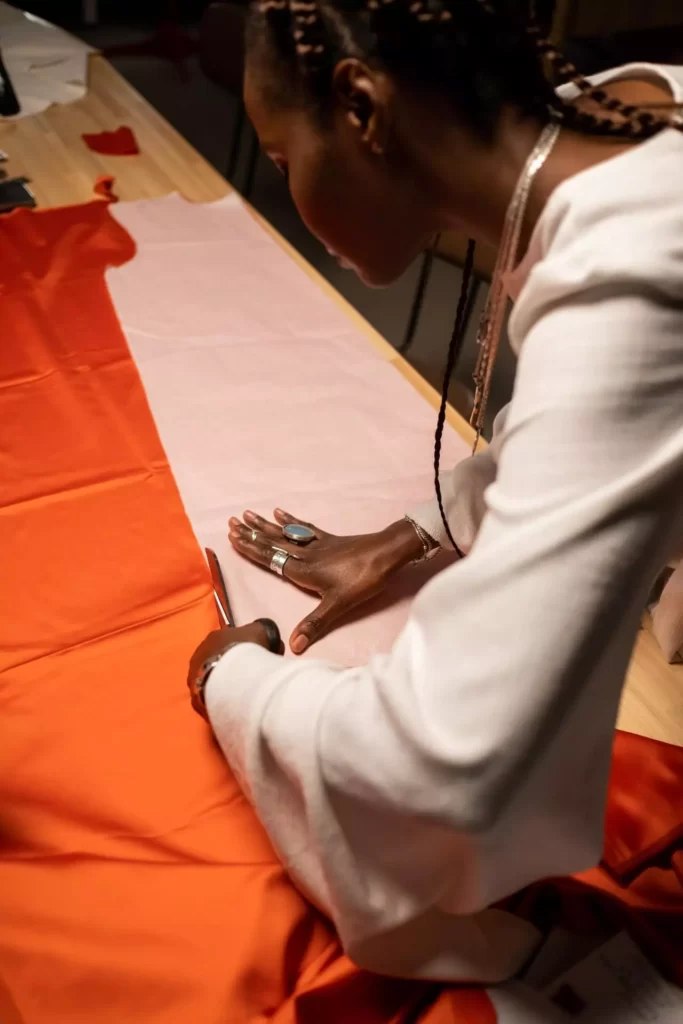
After complete marking, Lay the fabric or use a spreading machine for the next step, which is cutting the fabric. Arrange the fabric layers in the spreading machine, and bind those. For trimming, making pockets you may use this. The main operation of the cutting room is spreading and cutting. All of the operations in the cutting room are the most crucial, because at the point after cutting the fabric, there is left very little room for reviewing and fixing errors.
The main concern of planning to report the whole items in the cutting room shall be the same as those needed to keep full production in the tailoring room, according to the planned agenda. As I said any error that is created or ignored in the cutting room will affect the tailoring room hence the final garment. There are different types of power knives like Straight knives, Servo assisted straight knives, Round knives, Band and Fabric knifes. These are all manual, not computerized, though there are different computerized cutting machines also which I am not discussing any of them here. You can use a straight knife cutting machine for cutting purposes.
Let’s know little details on cutting.
The external line of the pattern piece accommodates a pattern for cutting the fabric. You can see an illustration of little scissors in the line sometimes. This is called Single Line Cutting.
You can see multiple illustrations like multiple solid lines, printed on the paper. These guides while cutting. This is known as Multi-Line Cutting. Sometimes there are shorter cutting lines for those design that has a shorter illustration, within the pattern.
Also, mark those garment parts or cut fabric pieces with a paper sticker. Assuming all ingredients of fabric, design, and trims are satisfactory and perfectly planned and cut, move to the next step towards manufacturing hence stitching room.
7. Manufacturing (Stitching-EMBROIDERY)
We finally came to the Manufacturing step within the garment manufacturing process. Embroidering or printing on the garment is done generally after cutting fabric parts. If you’re just starting your business you don’t have to spend on equipment for printing or embroidery. If your client wants this you can get help from the outside exchange of some money.
Stitching
Garments are sewn in an assembly line, with the garment getting complete because it progresses down the stitching line. Sewing machine drivers admit a pack of cut fabric and constantly suture an original portion of the garment, passing that completed portion to the posterior driver. For illustration, the primary driver may suture the collar to the body of the garment and thus the coming driver may suture a sleeve to the body. Quality assurance is performed at the edge of the stitching line to make sure that the garment has been duly assembled and which no manufacturing blights live. When demanded, the garment will be reworked or mended at designated sewing stations.
Embroidery
You may use a stitching machine for embroidery purposes without any outsourcing if and only if you know how to do it properly. Threadworks can be very beautiful if you know them. We often love something handmade. Clients often want embroidery works on neckline, hemline, waistline, top or chest area, in blouse.
Screen Printing
There’s also a printing process known as screen printing, which is transferring ink through the stencil onto the fabric. After screen printing the dry the fabric. Embroidery and printing both depend on the occasion and fabric types because not all the fabrics are for every work.
8. Garment Inspection
Inspection
This is the last but not least step of the garment manufacturing process before packing. If your project does not meet the client’s expectations she/he can even reject this. So be careful while inspecting a garment. It is better to show the client your design and a sample beforehand for big projects. For industries, there will always be a certain percentage of garments that appear with defects. Set a standard table of criteria for measuring quality. This is the best way to filter out. For increasing success rate calculate total production minus defects or quality product percentage. This is important to reduce wastage.
Laundering
Inspecting also involves laundering. It’s necessary to remove any flaws as well as any marks, spots, or stains that occurred during the marking cutting or manufacturing process of the garment. In big industries, there are costly washing machines for this purpose. But you can use lukewarm water or any chemical stain remover according because the client always wants washed garments. There are some special facilities like stone washing or acid washing. Don’t do washing without proper knowledge of the fabric you used.
9. Finishing
Let’s finish the process of garment manufacturing.
Trimming Threads
Newly finished cloth always have some uncut threads. These are generated by stitching or fabrics’ loose ends that are missed while cutting. While stitching, you may miss these uncut threads. No big deal, Examine and trim later.
Eliminating Loose Ends and Other Unnecessary things
I have talked above that in the sixth step cutting to label all the fabric pieces with stickers, so remove all of those stickers, because you don’t wanna see your client all those industrial labels.
Pressing
After trimming and eliminating loose ends now press the entire garment for a finishing look. Removing folds, wrinkles is very important to get a polished look because a non-pressed garment looks very poor. Even cheap cloth can look polished with proper pressing. One thing I forget to say before is please go through an under pressing method after cutting and seam allowance of every piece. Use heat and steam accordingly. You can or rather I’ll say you need to examine by pressing a sample fabric first because wrong temperature or heat can ruin a fabric/garment. You don’t wanna disaster. So always apply iron on a sample fabric first. Keep moisture amount also in mind.
Please check these three articles to get more of an overall idea of pressing.
- Pressing Types and Relation with Fabric.
- Essential Ten Pressing Techniques.
- Pressing Tips and Safety Precution.
10. Packing and Shipment
Folding
Folding garments is an art 😄 Hehe! No Joke. Fold the finished garment in a specific dimension. You can use templates for proper folding, you can find that on Amazon. Before folding attached price tags, washing caution tag if there’s any, the composition of different materials, etc. Folding types also depends on the type of garments because some heavy designer gowns, coats are not supposed to be folded yet you can fold shirts, skirts.
Packing
Pack the folded garment within a polybag. But I’ll suggest something towards earth instead of plastic. You may use cardboard, outside of a paper packing because it’ll keep the garment in the desired shape. Some products you can pack directly into the cardboard like shoes. If your client directly takes the product from you then this is okay, but if you are transporting clothes, then make multiple and use cartons for transporting finished garments.
Audit
Auditing is required if you’re running a business not just selling a single garment to your client. Auditing is done in all the companies. And even you don’t have a company but you’re working as a maker and wholesaler to do your audit before and after packing. Every carton shall have to mark how many packages are inside one carton, and then count the total number of cartons. Make sure not to pack any defective garments. One single item can be harmful to your business especially if it is small.
Complete!
Finally, the garments are ready for shipment and ready for the consumers, or your client.
I hope this was informative and helpful (❁´◡`❁) That's all for today! Please leave a comment!